How to calculate manufacturing overhead applied
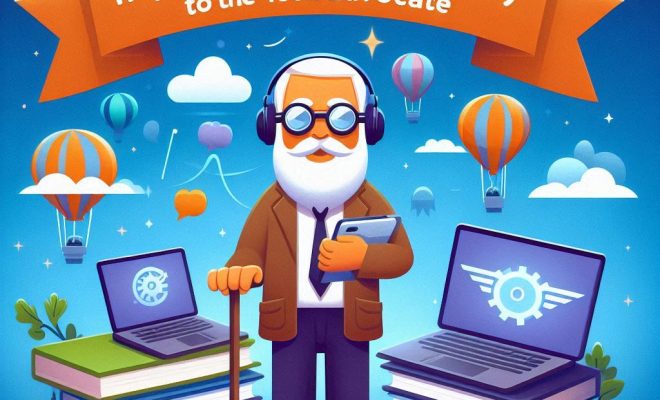
Introduction
In the manufacturing industry, understanding and calculating manufacturing overhead is crucial to controlling costs and ensuring the smooth progress of production. Manufacturing overhead, also known as factory burden or indirect costs, refers to all costs incurred within the production process that cannot be directly traced back to specific units of product. These costs include electricity, rent, depreciation of assets, supervisor salaries, insurance, and repairs. To better manage these expenses and establish accurate pricing strategies, businesses need to calculate the manufacturing overhead applied. This article will discuss the concept of manufacturing overhead applied and provide steps on how to compute it.
Defining Manufacturing Overhead Applied
Manufacturing overhead applied refers to the portion of manufacturing overhead assigned to a production department or cost center during a specific period based on a pre-determined overhead allocation rate. The actual amount of manufacturing overhead incurred may differ from the applied amount; this discrepancy gets reconciled through over-applied or under-applied overhead calculations.
Calculating Manufacturing Overhead Applied: Step by Step Guide
Follow these steps to accurately calculate your company’s manufacturing overhead applied:
Step 1: Determine Your Total Manufacturing Overhead Costs
The first step is calculating total manufacturing overhead costs for a specific period or accounting cycle. Include all indirect expenses associated with production such as utilities, rent, depreciation on machinery and equipment, factory maintenance, insurance, salaries for support staff, and taxes. Exclude direct materials and labor costs from this calculation.
Step 2: Choose an Allocation Base
An allocation base serves as a common denominator for distributing manufacturing overhead costs among various production departments or jobs. Typical allocation bases include direct labor hours, direct labor cost, machine hours, or units produced. Choose an allocation base that closely represents how your organization incurs manufacturing overhead costs.
Step 3: Calculate Your Overhead Allocation Rate
Divide your total manufacturing overhead costs by the chosen allocation base to determine your overhead allocation rate. This calculation is:
Overhead Allocation Rate = Total Manufacturing Overhead Costs / Chosen Allocation Base
Step 4: Allocate Manufactured Overhead
By multiplying the overhead allocation rate by the actual amount of the allocation base for each department or job, you can determine the allocated manufacturing overhead. The formula is:
Manufacturing Overhead Applied = Overhead Allocation Rate x Actual Amount of Chosen Allocation Base
Example:
Let’s assume a company has $100,000 in total manufacturing overhead costs, and it uses direct labor hours as its allocation base. The company estimates it will need 50,000 direct labor hours in its production process during this accounting period.
Overhead Allocation Rate = $100,000 / 50,000 = $2 per direct labor hour
Now suppose a specific department consumes 10,000 direct labor hours during this period.
Manufacturing Overhead Applied to Department = $2 x 10,000 = $20,000
Conclusion
Understanding how to calculate manufacturing overhead applied is vital for businesses to efficiently manage production costs and make informed pricing decisions. By regularly monitoring and adjusting these calculations as needed, companies can stay in control of their financial health and remain competitive in their respective markets.